
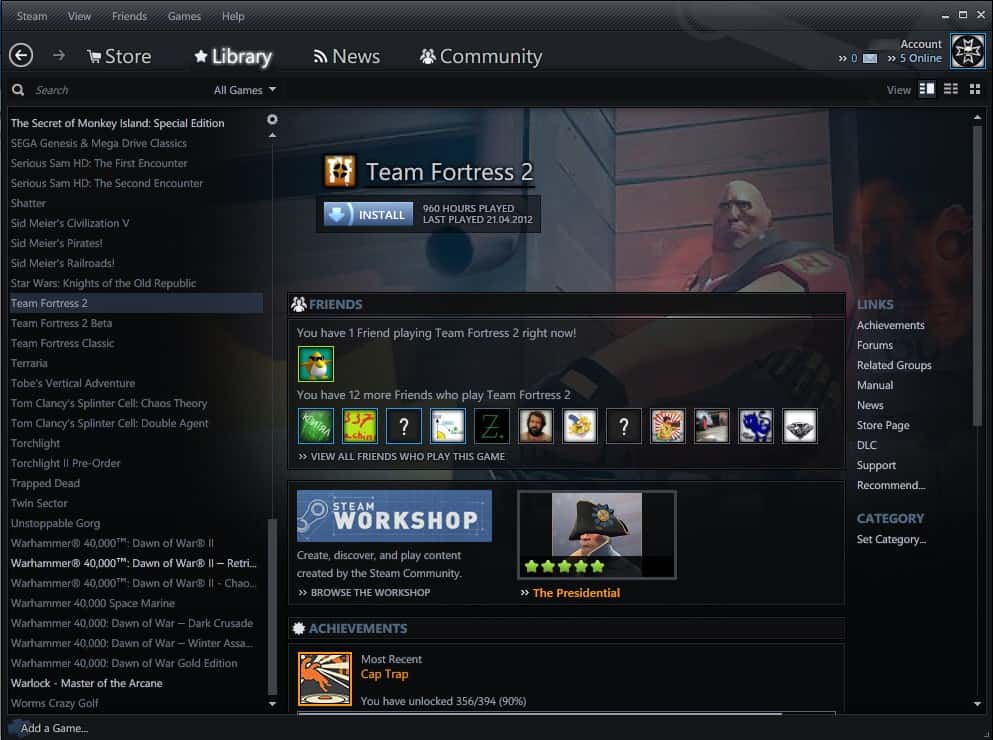
This will help to maintain thermal performance of the system throughout its service life.ĭirt is another major factor which must be considered when selecting traps. It is important that the pipework is designed and installed correctly. This subject will be dealt with in further detail in Block 13 - 'Condensate Removal' In this situation, the trap should either be complemented with a pump, or changed for a punp-trap. If there is a lift after the trap, there will always be a tendency for waterhammer, whichever trap is fitted. Temperature controlled heat exchangers can only work effectively if condensate is allowed to drain freely from them.

The bottom of any riser must also be drained. Two important applications are the drainage of steam mains, and of temperature controlled heat exchangers.Īs a general rule, steam mains should be drained at regular intervals of 30 to 50 metres with adequately sized drain pockets. The solution is to investigate and eradicate the true cause of the problem by correcting the system inadequacies. If a steam trap persistently fails on an established system due to waterhammer, it is probably the fault of the system layout, rather than the trap. Basically, however well a steam trap is made, if it is installed in a poorly designed system it will be less effective and have a shorter working life. This allows the steam trap to last longer under normal conditions, and will also be better able to withstand the effects of poorly designed systems. Modern design and manufacturing techniques have produced steam traps which are more robust than those of their predecessors. The inability of condensate to properly enter or travel along an undersized return line, due to either (a) flooding, or (b) overpressurisation with the throttling effects of flash steam.From an application which is temperature controlled and where condensate has to lift to a return line, or return to a pressurised system.Failure to remove condensate from the path of high velocity steam in the pipework.Waterhammer can be caused in a number of ways, including:. A more likely explanation is that a faulty steam trap has been damaged by waterhammer. Symptoms of waterhammer are often attributed to malfunction of the steam trap. The proper layout of steam pipework is also dealt with in Block 10 - 'Steam Distribution'. The Modules 11.6 to 11.11 inclusive 'Selecting steam traps' will deal with the correct matching of steam traps to applications and layouts.
#Larger than light steam install#
It is equally pointless to install the correct layout and not pay proper attention to steam trapping. It is often futile to install the correct trap for an application if the system layout will not allow the trap to operate correctly. This could be due to poor design of the steam and condensate pipework, the use of the wrong type of trap or traps or a leaking steam trap, or a combination of these factors. Waterhammer is a symptom of a problem in the steam system. Please refer to the following sub-sections in this Module for further advice on this matter. However, system design and maintenance needs will also influence performance and selection. The trap selection follows on the basis that the requirements of pressure, condensate load and air venting have been met, in the provisional selection. The basic requirements of good steam trapping have already been outlined but it is worth repeating that the performance of the plant is paramount. By definition, a steam trap must trap or hold back steam whilst at the same time not restricting the passage of condensate, air, and other incondensable gases.
